EOS 積層製造之模具隨行冷卻案例分享
在過去的幾年裡,汽車塑膠零部件的品質已大幅提高:複雜性、高擬合精度、視覺吸引力和表面觸感全部滿足對一流品質的不斷需求 —— 甚至是很多高價模型中的要求。製造商和供應商正在依賴越來越多的高科技解決方案。捷克共和國公司 Innomia a.s. 活躍的行業之一就是汽車行業。該公司已成為直接金屬雷射燒結 (DMLS) 優勢的積極宣導者。公司的產品組合包括原型結構、注塑模具和鑄造工具用嵌件的製造以及模具維修等。在 EOS 技術的幫助下,DMLS 專業人員已能夠支持汽車供應商 Magna 優化塑膠零件的生產過程。這涉及到冷卻過程的修改。此案例主要關注前座椅之間的扶手製造。
Innomia 的客戶 Magna,是汽車座椅扶手塑膠零部件的供應商。基於傳統注塑過程的生產,是一個非常複雜的過程,其中每個步驟必須完美運作,才能確認產品的品質。
液態基材的熱量需要透過製造工具消散,以使塑膠能夠固化。其中冷卻過程會影響零部件的品質,因為不規則的散熱會導致變形。除此之外,溫度控制對於決定生產週期時間具有非常重要的作用。散熱越快,即可更快地取出零部件,然後生產下一個零部件。
通常模具嵌件採用極其導熱的鈹銅合金製造,並且只能通過嵌件的一側進行冷卻。這意味著溫度分佈不均勻。冷卻水需要溫度非常低,僅 16 °C,以吸收熱量。嵌件表面高溫達 120°C,附近會產生濕氣,從而會加速腐蝕。這導致每一到兩周就需要進行成本高昂的清潔。模芯的硬度需要能夠防止定期清潔過程對表面的損壞。
Innomia 的設計人員開始研究新的模具嵌件冷卻系統,來優化生產過程中的散熱問題。團隊決定組合集成的精密冷卻通道、EOS DMLS 技術來進行嘗試和試驗。
模具嵌件的冷卻通道直徑僅 3mm。所選的金屬為馬氏體時效鋼 1.2709。根據三維資料分層應用並熔化金屬粉末的製造過程使得捷克專家員工能夠通過後期處理將硬度增加到 50HRC 以上。這些機械特性能夠保證高度耐磨,從而降低維護成本。
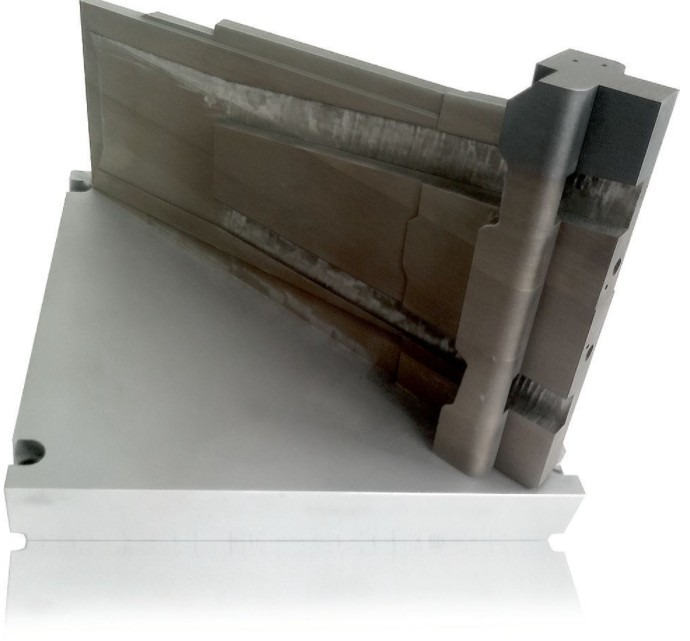
“DMLS 過程通過使用 EOS 金屬列印設備,使我們能夠製造極其耐磨的零部件,同時成功保持在設計方面的可靠方法優勢並縮短週期時間,”Innomia CEO Luboš Rozkošný 解釋說,“我們以有限的成本解決了生產過程的主要挑戰。”
使用積層製造技術實現的精密冷卻和生產達到了預期的結果。溫度分佈以及相關的散熱現在更加均勻。由於熱量會分散並且會更快地從模具和零部件中消散,因此 60 °C 的水溫足以進行冷卻—減少所需的能量。嵌件表面本身不會升溫到 90 °C 以上,使工程師可以進一步解決周圍區域的濕度問題。
由於 Innomia 和 EOS 技術,Magna 將維護週期延長至了 5 到 6 周。空氣濕度凝結和可能的模腔腐蝕問題徹底解決。均勻冷卻通道效果良好,使現在的生產週期所需的時間比以前縮短 17%。由於熱量分佈和散熱均勻、快速,零部件不再變形。這將對製造的品質和速度具有直接和積極的影響。生產週期縮短以及最終產品的品質提高是同時實現的了兩大好處。370,000 個迴圈之後,Innomia 和 Magna 進一步改善了結果。在這一期間,總成本節約已達到約 20,000 歐元。
Magna 模具維護主管 Pavel Strnadek 對這一結果非常滿意:“冷卻問題是我們長期以來一直試圖解決的問題。我們知道改善產品的外觀,但是卻不能完成製造。積層製造使我們取得了突破。我們能夠規劃所期望的冷卻通道,然後相應地製造模芯。雷射會逐層熔化金屬粉,因此能夠製造任何形狀。結果在每一層面都令我們信服。維護、最終產品的品質、成本、散熱 — 這是一個完美的項目。” — Škoda 的供應商 Magna 每天都在展示這一點。