EOS 塑料增材製造技術介紹
EOS 公司用來成型塑料零件的 3D 打印技術被稱為“選擇性雷射燒結” (SelectiveLaser Sintering 或 SLS),它屬於粉體熔化成型 (Powder Bed Fusion或 PBF) 技術的一種,運用雷射選區燒結零件的橫截面並一層一層堆積起來。
具體的工作方式為:首先加熱打印機的工藝倉到材料的成型溫度,然後透過鋪粉裝置或刮刀在打印基板上鋪上一層薄薄的粉(一般單層的厚度是 0.1mm 到 0.12mm)。鋪粉結束後,雷射光會隨著掃描鏡的偏轉在粉床表面選擇性地來回運作,雷射光所經過的區域粉末會被燒結在一起並固化。當所有零件橫截面區域都被燒結完之後,打印基板會下降一個層厚的高度。在雷射光沒有經過的區域粉末還是會保持原來的狀態為後面的層做支撐,這樣在零件上就省去了額外的支撐結構。接著鋪粉裝置或刮刀在原來燒結完的層上鋪一層新粉,雷射光再次掃描這層新粉並將其燒結在之前固化的零件橫截面之上。這個過程會一直重複直到所有零件都成型出來為止。
打印過程中粉末與燒結的零件共同存在一個缸中。由於一次打印可以同時成型多個零件,因此這種 3D 打印技術可以被用來做批量生產。每次打印為了使缸中的零件數量最大化,需要對零件的擺放和位置進行優化處理。
直到整個打印任務都結束之後,需要對存放零件和粉末的缸進行冷卻,當溫度降到一定程度便可以執行下一道工序——拆粉。拆粉的過程是將燒結成型的零件與未燒結的粉末分離,隨後要通過噴砂的方式清潔零件表面殘留的粉末。拆粉剩下的(未燒結的)粉末則可以被回收篩選給下一次打印使用。零件經過拆粉清潔後就可以直接使用,或者通過一些後處理方法增強其外觀效果或機械性能。
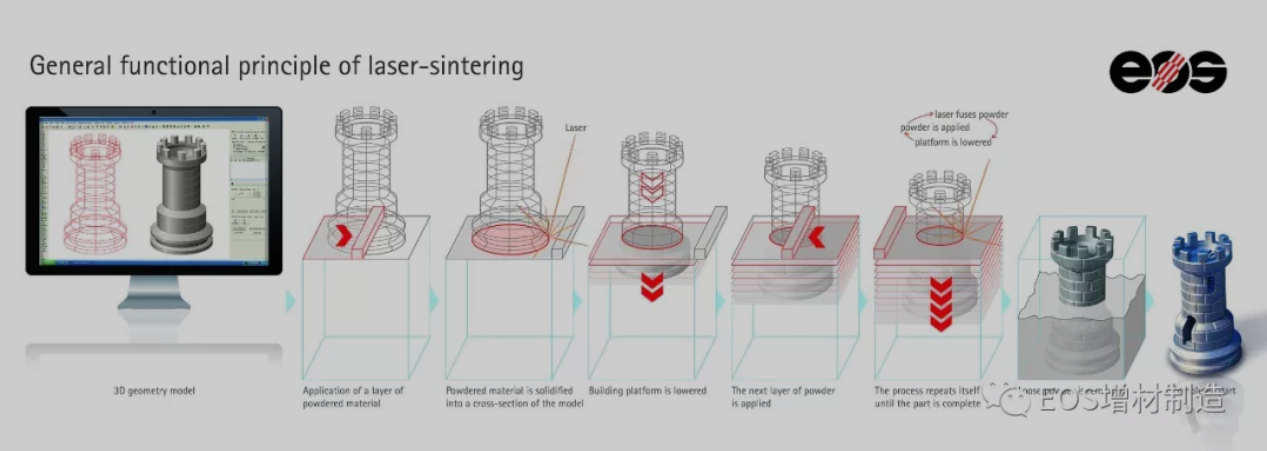
目前 SLS 技術被廣泛應用在工業 3D 打印中,尤其是製造一些功能原型件或最終產品。針對不同的應用,EOS 提供了不同的高分子材料作為選擇,比如聚酰胺(尼龍)、聚苯乙烯、以及熱塑性彈性材料。
雷射燒結的最大優勢就是零件在設計上幾乎沒有任何限制,因為缸內剩餘部分的粉末能作為結構的支撐,所以即使所生產的零件結構非常複雜也不需要額外的支撐結構。然而 SLS 技術的一個缺點就是生產結束後需要一定的時間冷卻,這樣會延長生產週期。
與其他 3D 打印技術的比較
迄今為止所有 3D 打印技術的過程都是把數字模型一層一層地製造出來形成物理實體。下圖顯示了目前市場上主流的 3D 打印技術,其中用來生產塑料零件最為常見的技術分別是 SLS、FDM 和 SLA。
熔融沈積成型 (Fused Deposition Modeling 或 FDM)
FDM 技術採用絲狀的線材作為成型材料。線材從卷線盤上被導入到 3D 打印機的噴嘴中,然後透過加熱噴嘴熔化材料。當材料變成熔融狀態後會被噴頭擠出並沿著電腦軟件預設的路線塗刷在基板或上一層成型路徑之上。材料被擠出後會立刻冷卻固化——這樣就能為下一層塗刷路徑提供基礎,直至整個零件被生產出來。
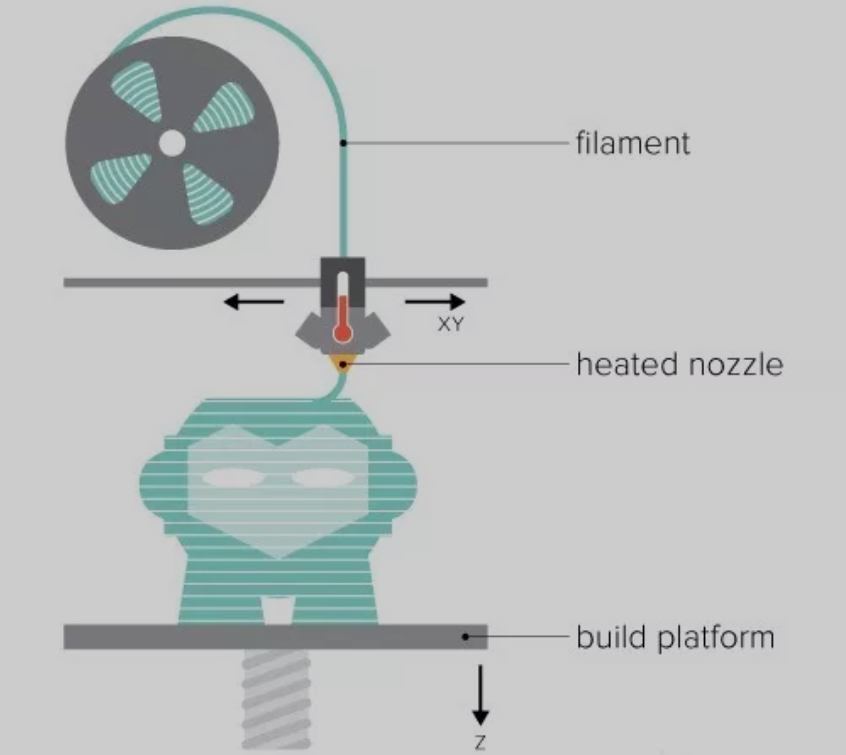
優勢和劣勢
作為市場上相對廉價的 3D 打印技術,FDM 能使用各式各樣不同顏色的塑料材料,包括 ABS、PLA、尼龍以及更多獨特的改性材料比如碳纖、銅或者木材。
FDM 技術為快速和低成本的原型件生產提供了一個非常不錯的選擇,並可適用於不同種類的應用。一個比較有創意的應用就是使用 FDM 3D 打印技術生產製造可以嵌入電子元器件並能直接使用的無人機外殼。然而由於成型工藝和材料上的限制,FDM 技術不太適合生產內部結構非常複雜的設計。
光固化成型 (Stereolithography 或 SLA)
光固化成型或有時候被稱之為數字光處理 (Digital Light Processing 或 DLP),它的成型原理是透過光源照射液態的感光樹脂材料使其固化最終形成 3D 物體,這裡的光源可以是雷射或者投影儀。
成型過程中,成型基板首先浸入到注滿液態樹脂的透明容器中。隨後,打印機內的光源把零件每一層的截面信息透過透明容器底部向液態樹脂映射,映射到的區域隨之便會固化。等到這一層完全固化後,成型基板會往上升一個層厚的高度然後光源再一次映射和固化新一層的液體樹脂。這個過程就這樣一直重複直到所有層都被固化,最終零件便被成型出來。
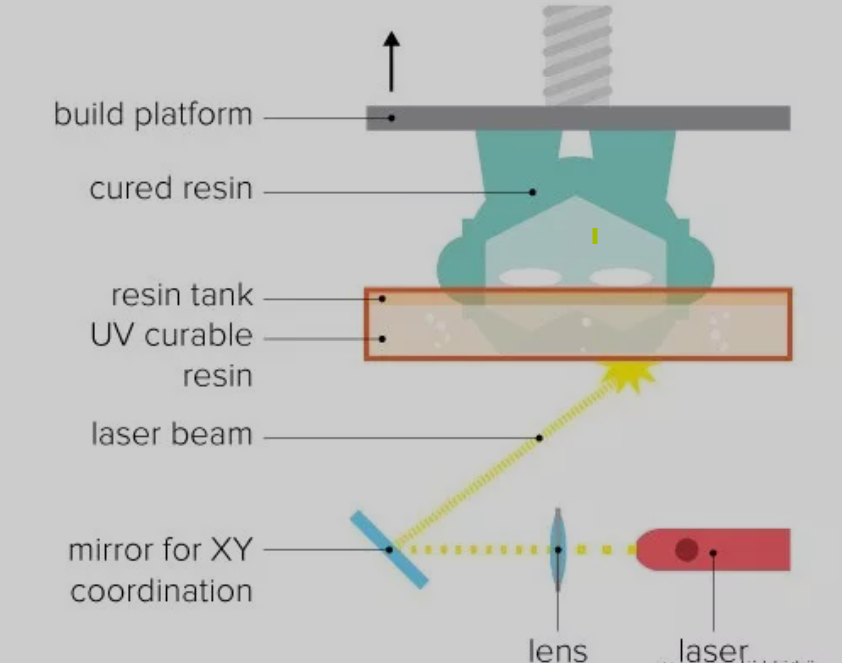
優勢和劣勢
SLA 技術所使用的材料僅限於光敏樹脂,但是近期有了一些新材料上市,它們能優化零件的力學性能或彈性。
採用 SLA 技術的 3D 打印機能夠生產出精度非常高、表面非常光滑的零件,一般普遍用於製作細節度較高的雕塑、首飾的模具、以及手板原型。由於他們的成型尺寸比較小,光固化技術不適用於打印大尺寸零件。
三種技術的對比
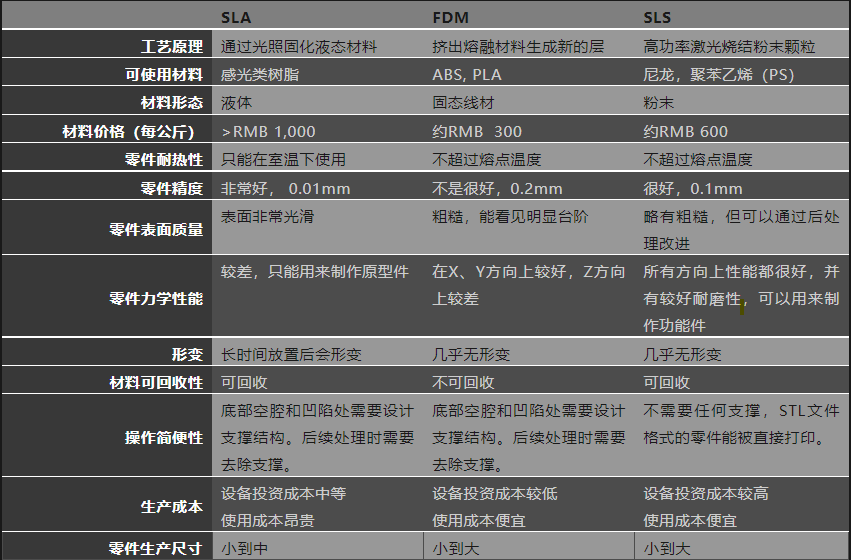