EOS技術促進了空巴A320neo引擎元件的高性價比製造
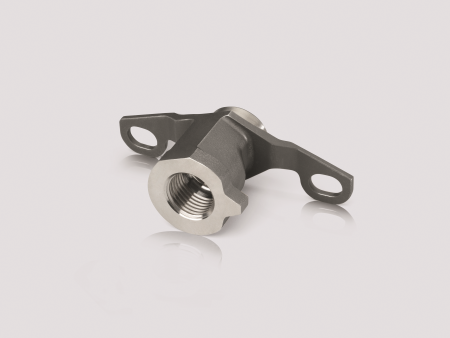
積層製造 PurePower® PW1100G-JM 齒輪渦輪風扇發動機的高速低壓渦輪機管道鏡支管台,用於A320neo 提供動力
(由 MTU Aero Engines提供)
油耗降低 15 % —這是製造商Airbus希望其短道中程飛機A320neo為客戶帶來的主要好處。為了實現這一目標,首先需要更高效的發動機。MTU Aero Engines 是美國發動機製造商Pratt & Whitney的主要供應商,為實現空中巴士的目標,為了保持在技術的最前端,慕尼克總部的航空發動機專家們積極支援使用創新的生產流程,積層製造在此起了重要作用,如在管道鏡支管台的生產中所示,管道鏡支管台是檢修渦輪機的進入點,是MTU使用EOS技術生產的產品。
挑戰
航空航太領域是世界上最具創新性的產業之一。僅僅憑藉A380的設計,Airbus就申請了380多項專利,適合批量生產的新材料和新技術,成本、重量和功能的等等考量,都在該行業扮演著非常重要的角色;因此,製造商和供應商們都在測試積層製造工藝的性能,在該工藝中,粉末經鐳射逐層硬化時便生產出元件。該方法最初是用於原型製造,因為它允許快速生產個別部件。然而,雖然其具有很多優勢,技術在批量生產中是主要關鍵。與該工藝相關的優勢包括提高了設計自由度和有大量的可用原材料,從重量極輕的防火/阻燃塑膠到各種金屬。一般來說,在飛機騰空而起的那一刻,成本和安全壓力都是非常重要的驅動因素;因此,在引進新技術時選擇適當的妥協和平衡非常重要。MTU Aero Engines是德國一流的發動機製造商,採用了逐步向積層製造過渡的策略。
“公司目前使用七套EOS設備。大約10年以前,我們就開始製造工具和開發元件。為了優化設備利用率和實施我們的階段性計畫,我們尋找更多可以應用該技術的領域。” — MTU公司快速技術部總監Karl-Heinz Dusel說。主要的挑戰包括成本和安全因素,同時還要追求戰略創新。
解決方案
管道鏡支管台將用於最新一代的發動機「齒輪渦輪風扇(GTF)發動機」—並準備用EOS設備來生產。
”第二階段初,我們開始生產原元件,用於取代現有的部件。用於A320neo-GTFs的低壓渦輪機的管道鏡支管台就屬於這一類。” Karl-Heinz Dusel
這些小附加元件允許技術人員通過管道鏡來檢查發動機內部的渦輪葉片情況。這些部件被鉚接在渦輪機外殼上,形成一個適用於內窺鏡(在航空航太領域術語中稱為管道鏡)的開口。
耐熱性和耐久性是使用鎳基合金的重要特性。這種高品質材料實現了元件要求的最佳效果,但卻很難加工。幸運的是,通過積層製造技術很輕鬆地解決了這類問題。由於MTU還是一家原材料生產商,該公司能夠開發新的工序鏈,已經趨於成熟並被集成到製造系統中。
整個製造工藝通過由MTU專門開發的一個控制系統支撐。線上監測可監控每個生產步驟和層級。此外,還引入了新的品質保證程式,如光學層析法。EOS設備甚至通過了德國聯邦航空管理局的認證。過去,管道鏡支管台是通過固體鑄造或銑削,但用於A320neo的齒輪渦輪風扇發動機的低壓渦輪機是第一個可以連續配備用積層製造技術生產的管道鏡支管台的渦輪機。最重要的是,EOS技術的成本優勢是決定性因素,不論是在生產過程中還是在開發階段。
結果
通過與EOS的密切積極合作,MTU的生產策略見到實效。批量生產管道鏡支管台的準備工作已經開始。假設每次作業16個部件,則每年總共可達2,000個部件。與以前的流程相比,節餘的百分比有望達到兩位數,並且品質達到較高的水準。MTU和EOS正在聯合進一步優化元件的表面加工,尤其是平滑的表面,目的是實現結構力學上的完善。
“EOS技術的特點是幾乎無限的設計自由度和顯著縮短了開發、生產和交付的時間。此外,開發和生產成本大幅降低。較輕重量和較大複雜性的元件可以成為現實,並且生產需要更少的材料和更少的工具。”
對於Karl-Heinz Dusel來說,優勢是顯著的。MTU看到了生產航空發動機結構的其他系列元件的巨大潛力,如軸承套或渦輪機葉片…等,它們都需要滿足最嚴格的安全性和可靠性要求。MTU的目標是15年內大部分組件應該使用工業3D列印技術來生產。因此,EOS積層製造技術有助於提高公司的競爭力,這在世界上最苛刻的行業中已經成為事實。