增減材混合加工真的可行嗎?
隨著積層製造技術的快速發展,其價值正被各行各業所認可。然而,工業級積層製造仍然面臨挑戰,例如提高零組件的加工精度以及表面粗糙度,面對這些挑戰,許多創新技術得到相對應的關注。其中之一就是增材與減材結合的混合加工技術。
這類技術主要原理為使用雷射來熔化金屬粉床上的金屬顆粒,並逐層建構出實際構形,同時在雷射燒結於一定層厚之後立刻進行銑削加工,透過切除多餘的材料來滿足較高表面品質的需求。隨後重複此過程,直到最終的零組件完成。這種技術結合了積層製造和傳統製造的各自優勢,因此自問世以來就一直得到了業界的廣泛關注。
然而,最近我們與某些客戶溝通時卻發現,採用其設備的客戶並沒有一間是按照上述過程操作此項技術。也就是說客戶還是必需先完成所有增材加工方才進行最終的表面加工。
為什麼會這樣?難道混合加工技術真的只是一種概念嗎?
經過一番仔細研究,總結出混合加工技術的幾項致命缺點,如下:
1. 混合加工技術忽略了熱處理的環節。
為了提高積層製造零件的結構硬度和強度,對零件進行熱處理是必要的。然而熱處理必然會產生些微翹曲或變形,因此將最終表面加工過程放在熱處理之後才是正確的選擇。
2. 銑削加工的碎屑問題。
另一個非常現實的技術問題就是在減材加工環節,銑削後產生的碎片掉落在粉床上會嚴重破壞粉床金屬粉末的微觀結構,進而導致在雷射燒結後零件產生品質缺陷,譬如零件拋光後有砂眼缺陷(“拖拽效應”)。如圖所示。
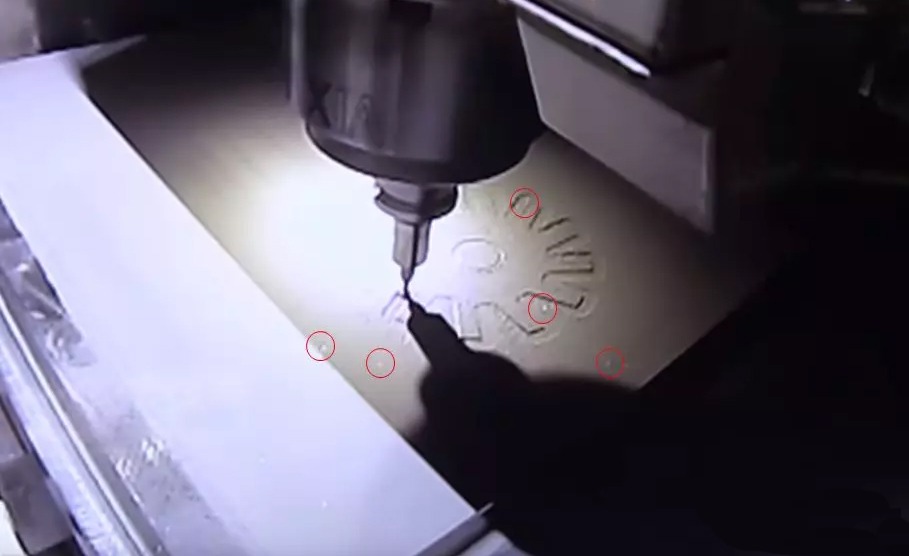
3. 加工效率的問題。
混合加工設備可能會有低效率問題。當增材模在進行時,減材模組實際上處於呆滯狀態,設備使用被大幅降低。量大的積層製造客戶在實際使用時發現,分開並行做加工才能發揮積層製造設備和傳統 CNC 製程的各自價值。而且提高效率的關鍵並非是把增減材設備生硬地強加到一台另設備裡,而是利用自動化手段提高從增材到減材的過渡效率。
綜合以上因素,EOS 公司經仔細研究之後,決定不再於混合加工設備上浪費寶貴的研發資源,而是聚焦於工藝開發,進一步提高積層製造的表面品質,同時透過對設備自動化改造,提升產品生產的整體效率。