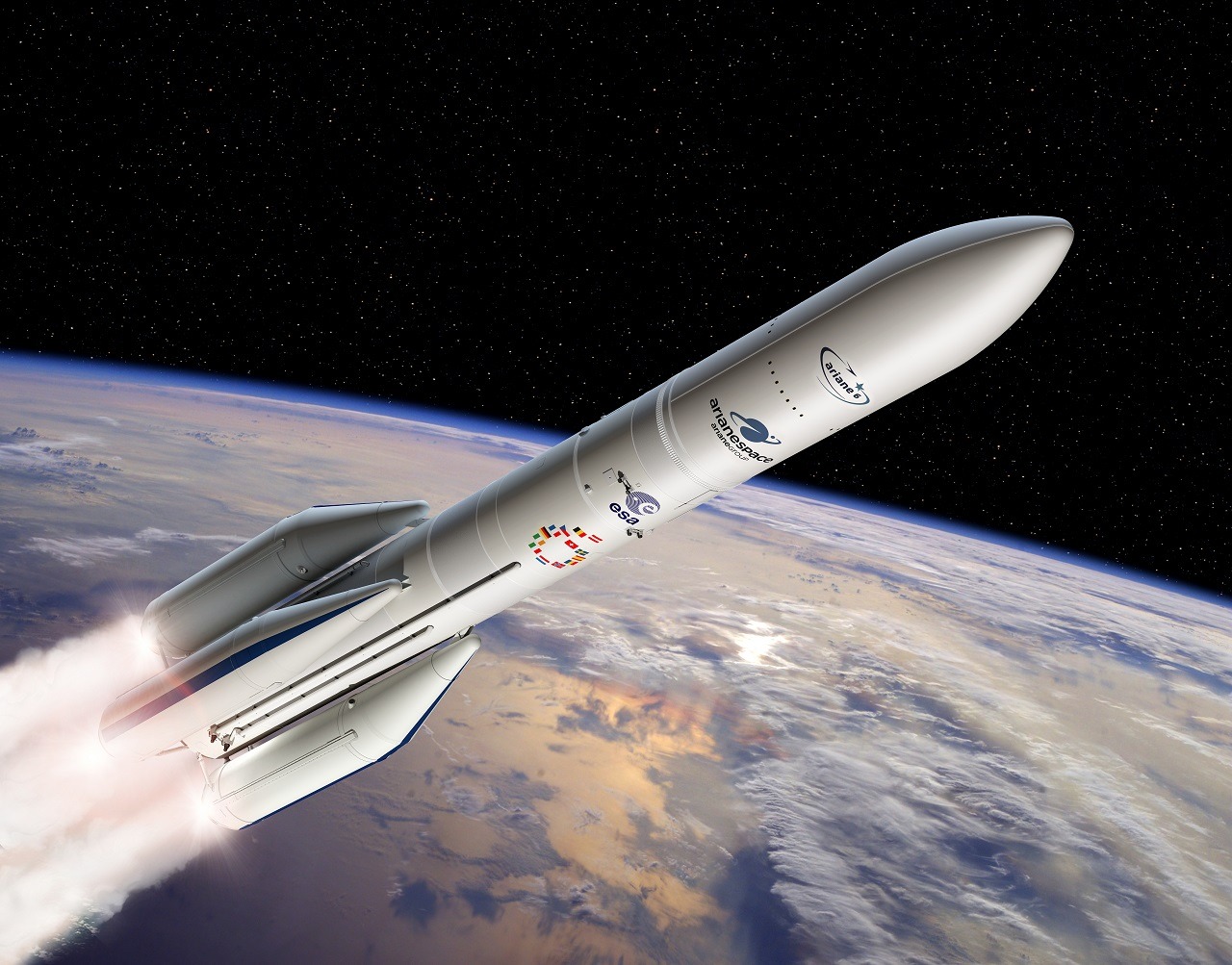
“任務關鍵”可貼切地描述用於航空航太行業的1類元件。耗資數億的任務由這類組件決定成敗與否,因此工程師們持續致力於開發品質、功能性和堅固性最為卓越的元件,同時簡化製造鏈並減少元件的數量;借助 EOS 技術,ArianeGroup 成功將其推向全新高度:面向未來的上級助推器中使用的火箭發動機噴嘴從原來248個元件減少為僅 1 個組件。噴嘴已經簡化為真正的一體化 (AiO) 設計。
ArianeGroup前身為空中巴士賽峰發射公司,是歐洲航空航天公司空中巴士和法國賽峰集團於2015年組建的合資企業。它由三大核心業務組成:航空航天(軌道推進系統和設備),國防和安全,以發展為目標並生產亞利安6號運載火箭。
歐洲航天局(ESA)希望借助高效的運載火箭技術在航太運輸領域佔據強而有力的獨立地位,為此委託ArianeGroup 打造新一代產品。Ariane 是歐洲航天局研製的一系列運載火箭,旨在將通信衛星等重型有效載荷送入地球軌道。
在推進模組中,會在極端條件下產生巨大推力,這需要在狹小空間內實現極高的可靠性和精確度。「噴嘴」是助推器的核心元件之一,負責將燃料混合物輸送入燃燒室。在傳統設計中,該元件由 248 個零部件構成,而這些零部件通過各種製造步驟生產、裝配而成,採用鑄造、銅焊、焊接與鑽孔等不同的工藝步驟可能會帶來缺陷,從而可能導致在極端負荷下產生風險;生產如此多的零部件也是一個十分耗時的複雜過程,在噴油器元件領域,傳統的生產過程需要在銅套管中鑽出 8000餘十字孔,然後用螺釘將銅套管精確地固定到 122 個噴油器組件上,以便將其中流動的氫氣與氧氣混合;實現將所有零部件於一體的功能集成元件顯然是一項宏偉的目標,特別對於 1 類元件,這還有助於發揮巨大的經濟潛力,減少工藝步驟並縮短生產時間。
積層製造為這些挑戰提供了解決方案,若要生產一體化噴嘴,只能採用 EOS 技術,ArianeGroup 材料與工藝生產技術主管Dr. Steffen Beyer 博士解釋了為何選擇工業 3D 列印技術的原因。只有積層製造可以將功能集成、輕量化結構、更為簡單的設計以及更短的交付週期等特性融合於單一組件中。專案團隊再次選擇了耐高溫、耐腐蝕的鎳基合金 (IN718) 材料,該材料在高溫下可呈現出優異的抗拉伸性、耐久性、抗蠕變性和抗斷裂強度,並將與全新的生產技術搭配使用。
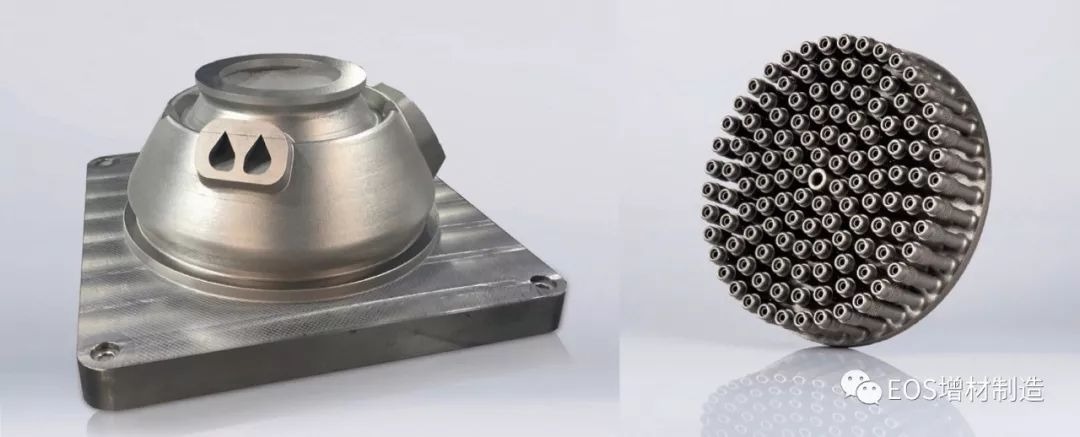
“成功開發出元件後,我們將我們的注意力轉向如何提高成本效益。”材料與工藝生產技術部門Dr. Fabian Riss博士說道。ArianeGroup的關鍵需求是縮短交付週期並降低單位成本。最初採用 EOS M 290 透過積層製造技術進行生產。初步試驗成功後,採用大型的EOS M 400-4系統進行量產。借助 4 雷射器技術,推進模組的製造速度可達原來的四倍。
“採用生產率較高的 EOS M 400-4 系統擴大生產,是我們為提高 Ariane專案的工業化和競爭力邁出的重要一步。憑藉EOS員工的豐富經驗和行業專業知識,協助合作得以高效展開,結果不言而喻,同時也有力證明了團隊的卓越表現。”
Dr. Steffen Beyer 博士補充道。
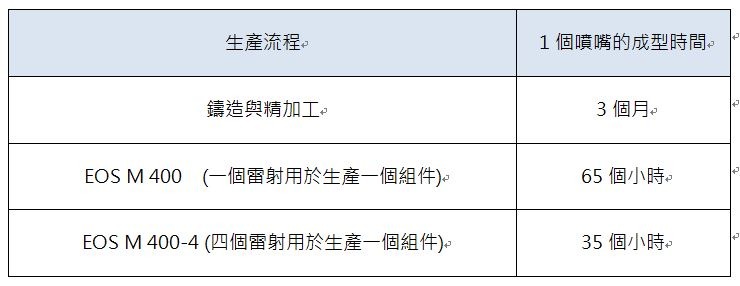
採用積層製造技術生產出的全新噴嘴令人驚歎,不是248個零部件,而是由 1 個組件構成,且功能相同,但大幅縮短了所需的生產時間。
借助EOS基於粉床融熔的工業3D列印技術,可將122個噴油嘴、底板和前面板、帶有相應進料管的圓頂氫氣氧氣燃料輸送頭列印為單個集成元件,以一體化成型的噴嘴為例,與單雷射器系統相比,EOS M 400-4四雷射器系統生產率明顯更高,可將成型時間縮短為3倍,成本降低50%。
專案團隊還取得一系列成功。與鑄件相比,設計得以簡化,材料性能得以提升,採用積層製造技術可大幅減小壁厚,而不會對強度造成任何損失。此外,組件重量大幅減輕,也能進一步縮短成型時間,從而降低成本。
最後但同樣重要的是,積層製造工藝可大幅加快創新週期。開發階段中的結構改進、設計修改和測試件的製造均可利用CAD 資料直接投入生產,工程師無需像鑄造零部件時那樣花時間準備模具。因此工業3D列印可大幅縮短交付週期,過去每次更新換替代通常需要半年左右的時間,而現在只需要幾天。除此之外,製造鏈產線現在已佈局於ArianeGroup工廠內部。
“Ariane 專案是我們的創新力與EOS專業知識的結晶。我們攜手合作,採用積層製造技術生產出火箭發動機的噴嘴頭,並取得了豐碩的成果:生產時間大幅縮短,成本降低50%。”
Dr. Steffen Beyer 博士
Ariane Group 材料與工藝 生產技術主管