3D 列印在壓鑄模具中的應用
翻譯:吳懷安、王浩
譯者注:本文原文為日文,由日本愛信精機(アイシン精機株式会社)的野村泰弘先生完成,發表於 2017年 5月。此文發表後,在日本工業界引起了廣泛的注意,並顯著促進了日本模具行業對 3D 列印技術的重視。這裡特別將該文譯為中文,供國內模具行業從業人員參考。受翻譯水準所限,如有錯漏,敬請諒解。
需要指出的是,由於原作者並未使用 EOS 標準參數,其列印產品的性能也存在一定缺陷,譯者在翻譯過程中通過注釋的方式予以了說明。
以下為原文翻譯:
近年來,隨著汽車零件設計向輕量化和模組化發展,使用壓鑄工藝的零件特徵也開始趨向於薄壁,且凹凸形狀開始增加用於剛度的補償。這一趨勢使得模具的冷卻設計變得更為複雜。並且,伴隨低成本廣泛化導致生產效率必須提升的現實情況,強化模具的冷卻能力成為了當務之急。
以前,模具冷卻只能採用機械加工的方式加工直線型的冷卻孔。但是受到加工方式以及模具強度的限制,冷卻孔在高溫部位的合理配置一直是個難題。
在此我司 (譯者注:這裡指愛信精機) 開始著眼於採用金屬堆積技術加工 3D 冷卻水路。所謂金屬堆積技術,就是採用雷射照射金屬粉末使其融化,一層層堆疊使之立體成型的技術(如圖一)。由於此造型技術可以完全再現 3D 特徵成型,所以採用複雜冷卻水路製造模具成為可能。但是,由於擔心材料本身的強度不足,所以,現階段在壓鑄領域的廣泛應用並沒有被很好的拓展。
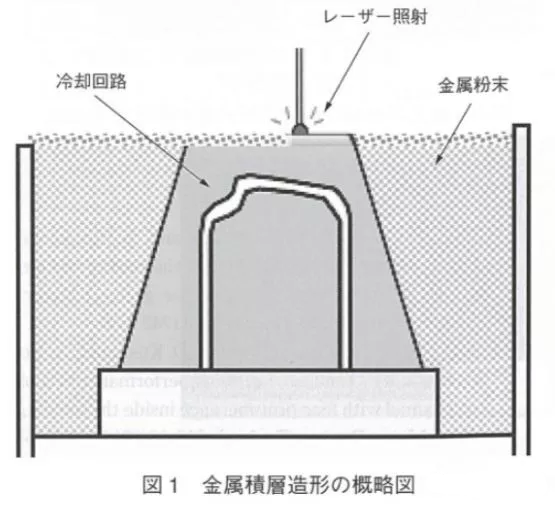
為了驗證材料的機械特性,我們進行了拉伸、疲勞試驗。選擇壓鑄模具 (JISSKD61) 作為對比材料。
試驗片採用圖2 所示的 2種形狀。以下如圖所示分為縱向與橫向。由於堆積材料通過熱處理可以得到較高的強度,所以採用馬氏體時效不銹鋼。金屬粉末堆積成型後實施熱處理,使之硬度達到 45HRC。
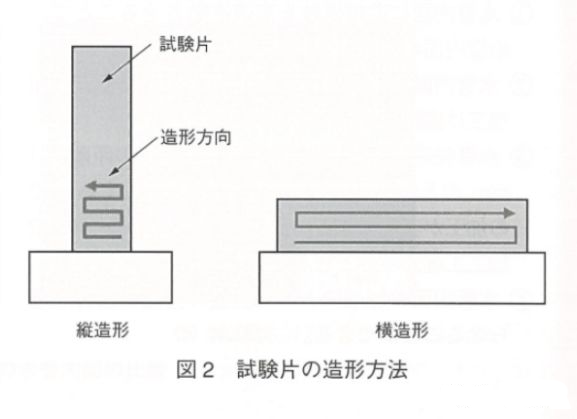
試驗結果:拉伸試驗採用油壓伺服式萬能試驗機。圖3 為拉伸試驗結果。在 0.2%耐力和拉伸強度條件下縱向試驗片同 SKD61 相比,結果相差大約 20% 左右,但是橫向試驗片只是相差幾個百分點。
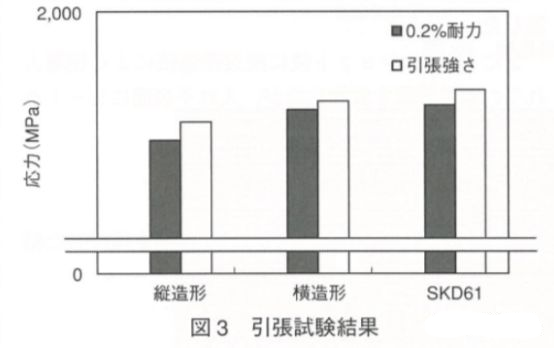
疲勞試驗採用小野式翻轉試驗機實施。圖4 為試驗結果。疲勞耐力限度 2%,同拉伸試驗一樣,縱向造型同 SKD61 相比相差約 40%。
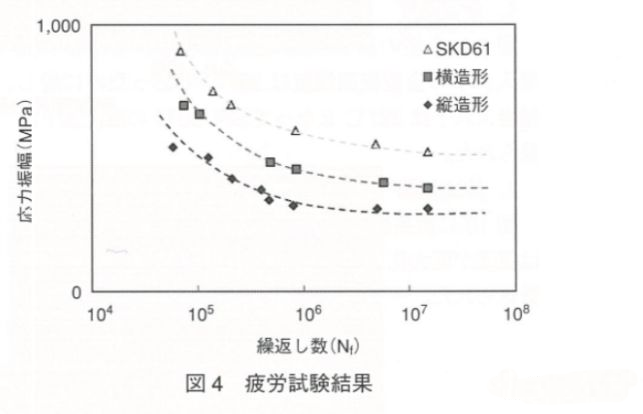
初步驗證的結果證實,金屬堆積的機械性能縱向劣於 SKD61。另外,與水準模型相比,顯示出機械強度在垂直建模中是各向異性的,因此強度有所下降。為了確定這些現象的原因,我們觀察了樣品的結構。
圖5 為金屬堆疊材料的橫截面。我們確認到金屬堆積材料在鐳射照射後形成的熔融池痕跡橫向排布並被層層堆疊。雖然在組織中,空隙缺陷沒有觀察到,但是確認到在堆積介面存在 Ti 和 O 為主成分的物質的生成。我們認為,這樣的物質有可能促進了龜裂的發展,最終各向異性影響了機械特性。
(譯者注:雖然原作者在文中並未詳細描述其列印參數設置,但從原文圖5 的圖片中,我們分析該作者採用了 50μm 以上的列印層厚,我們認為這是導致其縱向造型抗拉強度與標準試棒相差較大的主要原因之一。根據 EOS 官方進行的大量測試,按照 EOS 標準工藝參數設置後,縱向造型的抗拉強度與標準試棒相比差距不會超過 10%)。
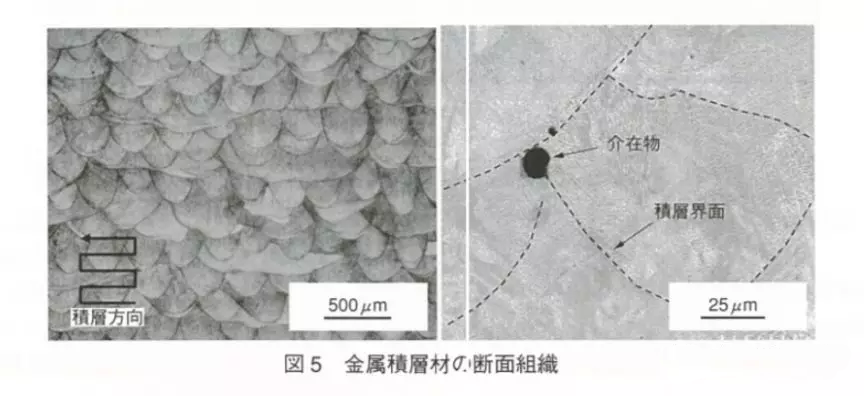
對於壓鑄模具的運用
1)適用部位的選擇:
如圖6 所示的曲軸箱模具鑲件為採用金屬堆疊技術生產的鑲件 (以下,稱為堆疊鑲件)。此次驗證採用成型位隨形冷卻以及直下式進出水,以前每加工 500 必須回火除去模垢。
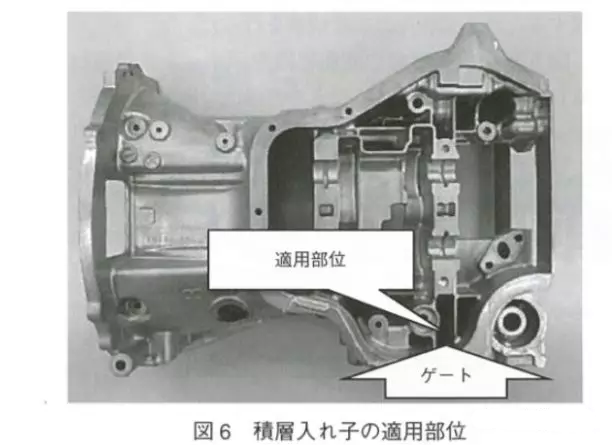
圖7 為適用部位的冷卻回路。鑲件配備採用傳統機加工的直線式冷卻孔 2處,但是冷卻效果有局限,冷卻孔之間產生模垢。在此之上採用堆疊技術將 2 路冷卻孔相連。3D 冷卻回路的設計參考了之前驗證的結果疲勞曲線圖 (圖8)。
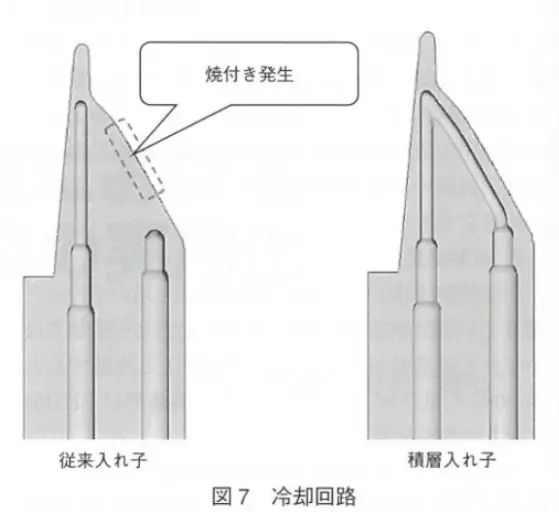
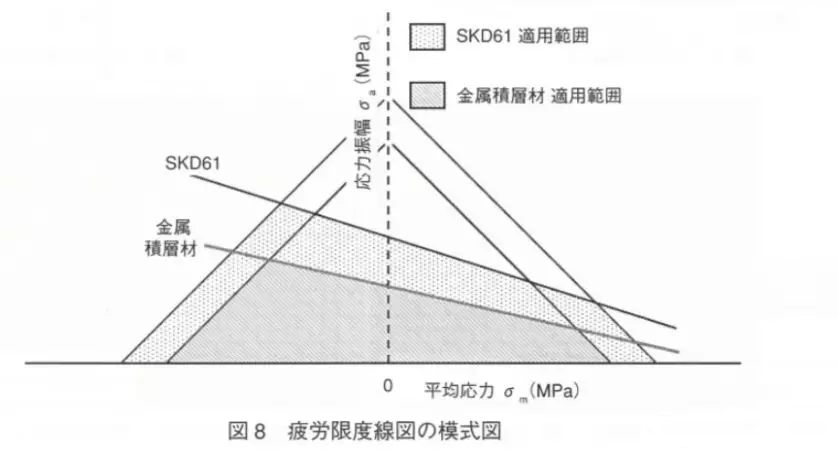
2)確認效果
圖9 為模具表面溫度 (開模後立即測量)。傳統鑲件的表面溫度為 387度,堆積鑲件為 297度,約下降了 90度。
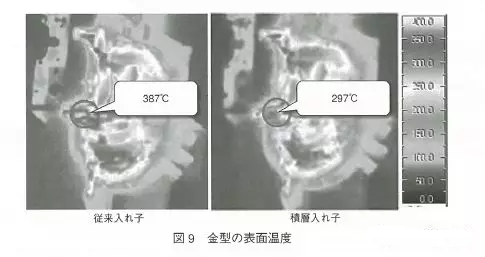
3)鑄造組織
圖10 為產品表面的截面組織。傳統鑲件的組織粗大化,這是由於凝固延遲發生縮孔現象。但是,堆疊鑲件組織細密化沒有發現縮孔現象。
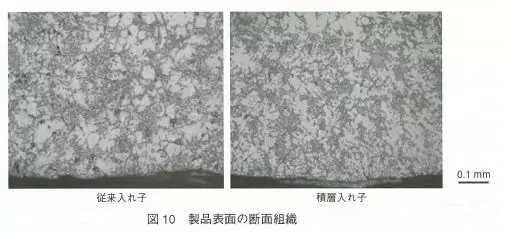
4)耐久性
圖11 為鑲件的外觀。傳統鑲件在加工 500次後必須回火除垢,堆疊鑲件加工 500次後無需回火除垢,在此之上加工 60,000次後也無模垢產生,免去了回火除垢的工藝。另外,加工 60,000次後採用浸透探傷法確認了堆疊鑲件,鑲件表面確認沒有發生熱裂紋。
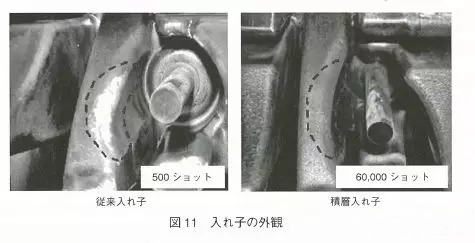
針對金屬堆疊材料在壓鑄模具領域的適用驗證結果,得到以下結論:
- 透過之前驗證的結果,金屬堆疊材料的機械性能與 SKD61 相比,縱向性能略差,這與各向異性有關。
- 透過瞭解金屬堆疊材料的特性設計冷卻回路,實現了壓鑄模具領域的實際運用。
- 採用 3D 冷卻回路實現了超高的冷卻效果,並且抑制了模垢的發生。