EOS Additive Manufacturing provides footwear designers with unlimited freedom of design. It is suitable for rapid prototyping as well as allowing product variants to be manufactured cost- efficiently in serial production using high-quality materials.
New Balance Athletic Shoe, Inc., has turned to design-driven manufacturing for 3D printing custom spike plates for their elite athletes, all based on an individual runner’s biomechanics and personal inputs. Using a proprietary process to collect race simulation data from Team New Balance runners, the Sports Research Lab then applies advanced algorithms to translate this information into an optimized design that can be manufactured additively by use of EOS technology.
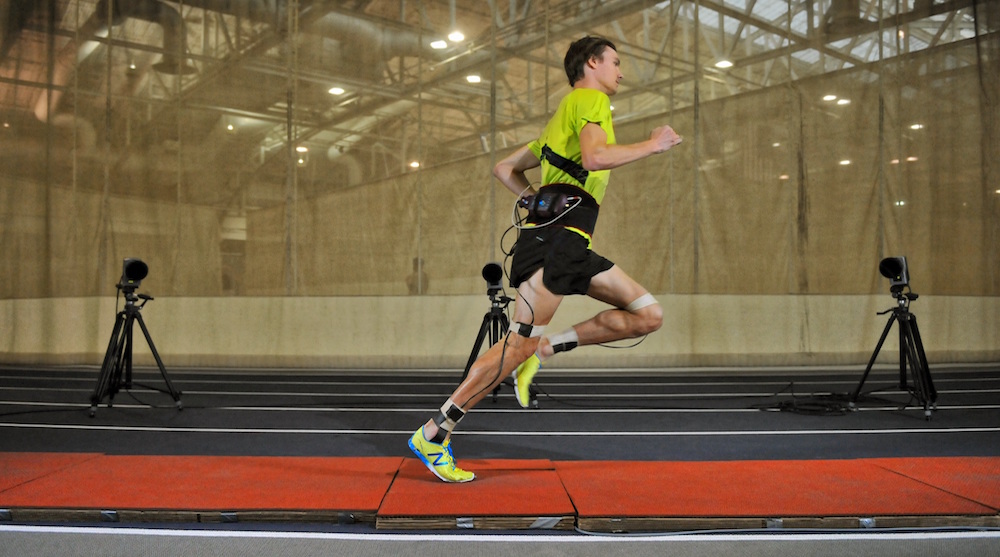
Challenge
No two runners are the same. This is especially true for athletes competing at the most elite levels. From their foot-strike patterns (the amount a runner’s foot rolls inward with each step) and braking and to their propulsion forces – every athlete is unique. However, the extent to which most running shoe models vary is rather limited by comparison. As a result, there are some who believe that customizing runner’s shoes, specifically the spike plate that provides traction on the underside of the shoe, can help these athletes become faster on the track. A proponent of this trend is New Balance.
Solution
New Balance was searching for an optimized process – and found it in EOS technology. Long before the spike plates are additively manufactured, or even designed, New Balance’s Sports Research Lab collects each runner’s biomechanical data using a force plate, in-shoe sensors, and a motion-capture system worn by the runner. This motion-capture system helps determine the relationship of the foot to the force plate, creating a three-dimensional vector map of the impact of each stride. The in-shoe sensors show distinct pressure indicator over the length of the runner’s foot strike as well as how the runner’s foot interacts with the shoe. When a particular part of the foot exhibits high-pressure values, it generally indicates that the associated 3D vector is important to that area of the shoe at that specific moment in time.
“We establish a relationship between these high pressures and the corresponding forces to help us create a map of forces relevant to each area of the foot,” says Sean Murphy, senior manager of innovation and engineering at New Balance. “A simple example is in the toe area. Generally, when you see high pressure there, it corresponds to a force that is pushing toward the heel to create forward propulsion. We use parametric modeling software to process this data and distribute the position of the spike plate traction elements, calculate the orientation and adjust the size of the elements, and incorporate specific runner preferences into the design.”
The designer is then responsible for performing the CAD cleanup necessary to create the final product, including touching up model surfaces and making adjustments to accommodate the full-size range of the spike plate. Once the final geometry has been verified, the CAD files are converted to .stl files and uploaded to the EOSINT P 395 system for Additive Manufacturing.
New Balance worked with high-performance materials manufacturer Advanced Laser Materials (ALM), part of the EOS family, to develop a proprietary nylon blend. The spike plates are built layer-by-layer in the EOS system using the custom-blend nylon powder coupled with tailored laser conditions to yield maximum engineering properties. “We decided to collaborate with ALM on this project because they had experience developing the type of material we were looking for,” says Murphy. “We had worked with them on a previous prototyping project and the variety of materials as well as knowledge that they offered made them the perfect partner.”
Results
“By additively manufacturing our customized spike plates we can manufacture on demand, fluidly adjust our process to accommodate different sizes and widths, and update designs without the continuing capital investment required by injection moulding,” says Katherine Petrecca, business manager of New Balance Studio Innovation. “The incorporation of the additively manufactured spike plate also allows us to realize a 5% weight reduction compared to traditionally manufactured versions.”