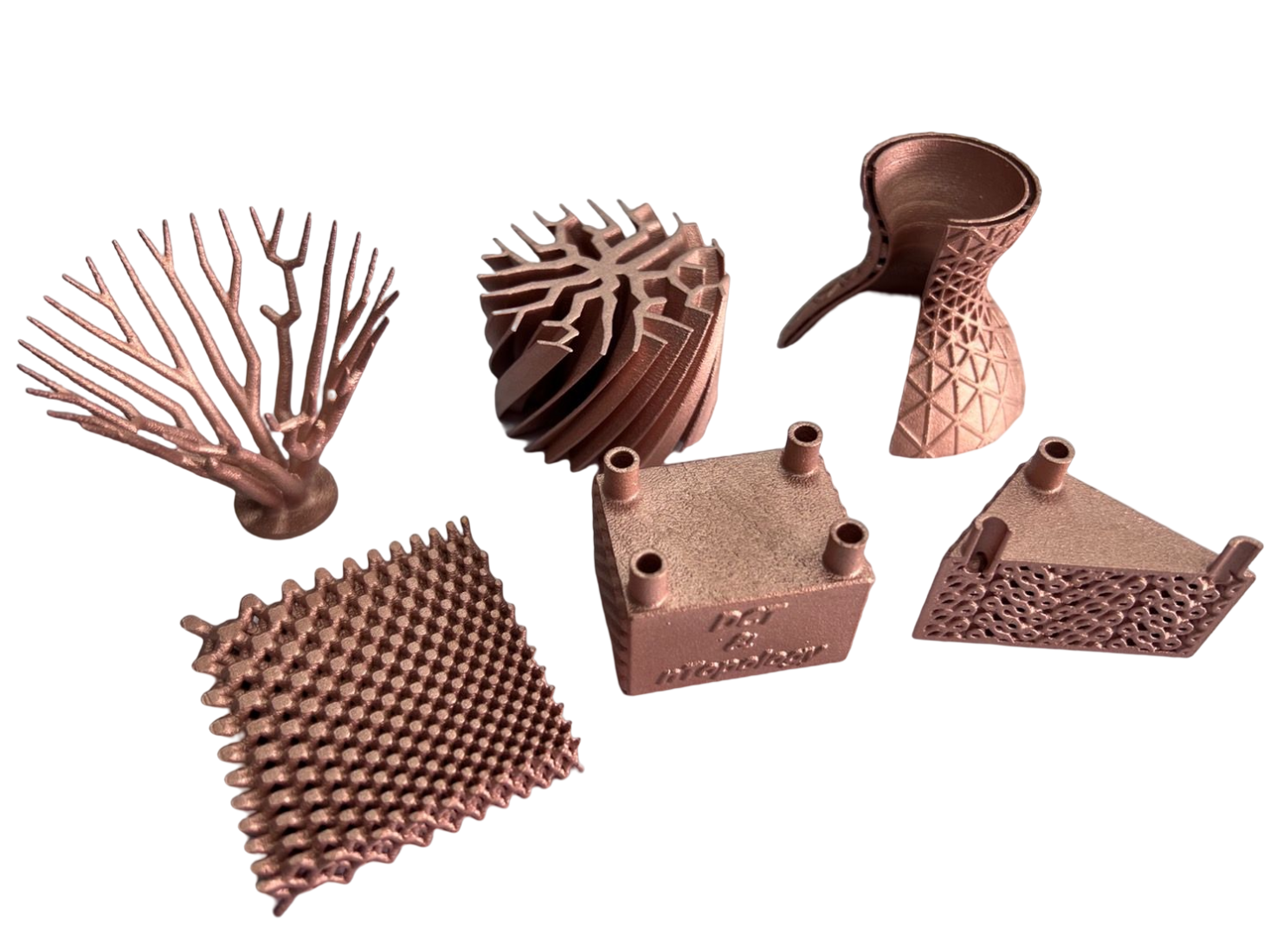
EOS AMCM M290 1kW additive manufacturing equipment system, combined with nTopology software, has successfully printed complex structures using EOS CuCP (>99.95 % pure).
“Pure copper” is an ideal material for heat exchangers and electrical components due to its thermal and electrical properties. Heat exchangers were often made from thin sheets of material that are welded together, this makes traditional production challenging and time-consuming. Additive manufacturing (AM) systems can build parts layer by layer, making the process more attractive for building heat exchangers. In addition to conducting heat and electricity, copper also has well-ability to resist corrosion and can even kill bacteria and virus. As 3D printing opens up more applications and possibilities, demands for complex copper parts is growing.
Metal cloth
Metal mesh
Breathable metal
Heat sink fin(wave)
Triply Periodic Minimal Surface(TPMS) – Diamond
Triply Periodic Minimal Surface(TPMS) – Gyroid
nTopology software was used to generate Triple Periodic Minimum Surfaces (TPMS), which have shown to be the best ideal for heat exchangers as they typically require maximizing surface area within a given volume. The design criteria for the TPMS gyro structure are 0.35 mm wall thickness and 2 and 5 mm cell size. nTopology software was used to slice the design into 30-micron layers and export borders and hatches as CLI files, which were then imported to generate build files for the AM process. The excellent thermal and electrical conductivity of EOS CuCP makes it ideal for a wide range of applications from electronics to heat exchangers, radiators and engine parts. Additive manufacturing of copper components also offers designers new degrees of freedom, allowing optimal functionality with few constraints.
Booster nozzle of rocket
Branched cylindrical fin
Branch lattice
Field-driven lattice
Box plate heat exchanger
Heat sink fin
nTopology has critical tools for thermal design
High-performance heat exchangers find applications in aircraft and road vehicles, industrial facilities and energy production, electronics cooling, and precision manufacturing.
Anatomy of a 3D printed heat exchanger
Heat exchangers may vary in type, shape and sizes, but the basic layout stay the same. Followings are the basic elements of a laminated heat exchanger.
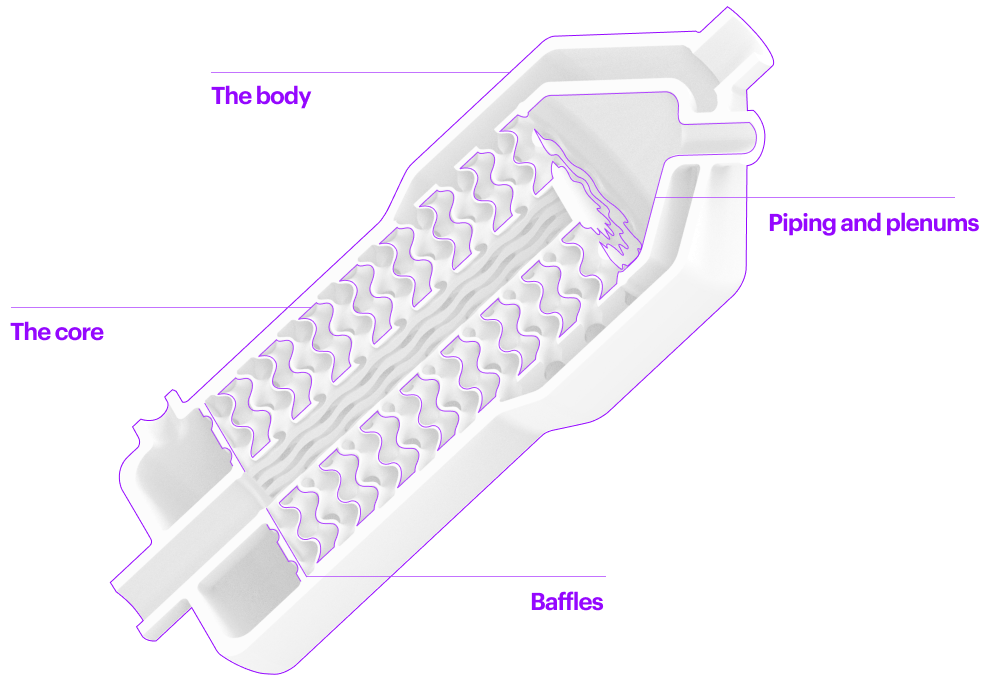
The Body
The Core
Piping and Plenums
Baffles
The shape of heat exchanger depends on the design space availability. While traditional form still offers high performance, with more freedom in external dimensions .
The core of the heat exchanger is usually filled with mesh. TPMS structures, like gyroscopes, yield the best results for liquid-to-liquid heat exchangers.
Inlet and outlet ducts and plenums gradually introduce fluid into the heat exchanger and act as pressurization buffers. Their geometry can be optimized using CFD data
Baffles are used to prevent mixing of cold and hot flows. They are usually introduced at the ingress and egress of the core.