PrintRite3D® INSPECT™3.0
Sigma Labs to Unveil PrintRite3D INSPECT® 3.0 at Formnext 2017
Sigma Labs has developed and released its next generation PrintRite3D INSPECT® In-Process Quality Assurance™ (IPQA®) software – Version 3.0. This release includes software enhancements and hardware upgrades and completes our migration to a distributed web-based application. Our newest release contains the industries most advanced set of IPQA® analytics algorithms that enable future generations of closed loop controllers. The PrintRite3D INSPECT® 3.0 software is now available for Multi-Machine Single laser systems, providing customers with one portal for monitoring their entire AM lab. Single and multi-machine, multi-laser configurations are in development with our OEM partners and as third-party add-ons.
PrintRite3D INSPECT® 3.0 software features 3D Thermal Mapping and Imaging tools as well as our exclusive TED™ (Thermal Emission Density™) powered advanced analytic engine designed to meet the needs of users focused on research, development and qualification-level activities. The researcher tools utilize raw sensor feature data without the need for baseline comparisons providing users the data and framework for limitless analysis. Quantitative, in-situ thermal history maps can be used to validate modeling and simulation (M&S) results prior to process characterization studies, process qualification & validation phases, as well as in conjunction with design optimization evaluations.
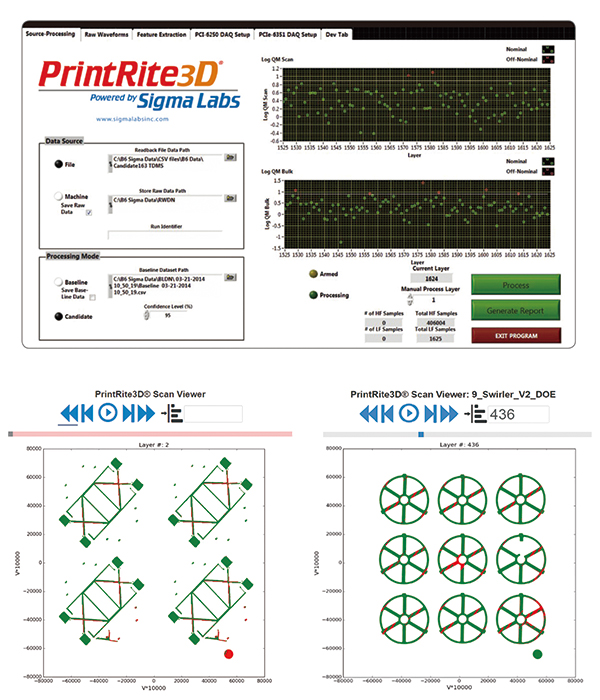
FEATURES :
- Part by part, layer by layer real-time melt pool TED™ data
- High resolution 3D thermal part map
- No baseline data sets required
- Client-server hardware architecture with a single viewing portal for monitoring multiple machines across an entire manufacturing organization
BENEFITS :
- Enables rapid qualification of metal AM
- Confirms modeling and simulation predictions using high resolution thermal history data
- Documents key process input variations on geometry
- Accelerates parameter optimization for optimal thermal conditions
- Allows design optimization to eliminate high stress concentrations
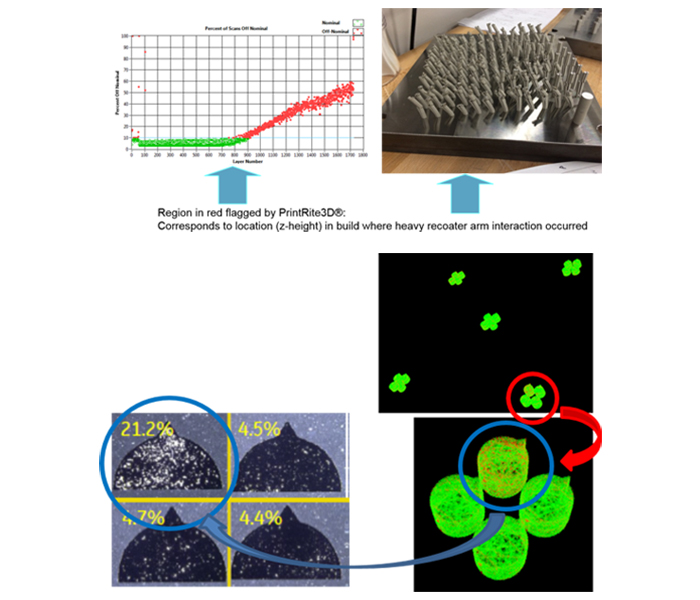